story by | |
photos by | Steven Hertzog |
OPEN A PDF OF THE ARTICLE |
Balancing business and science helps these KUIP companies create quality, reliable products as well as improve upon products already being used in today’s society.
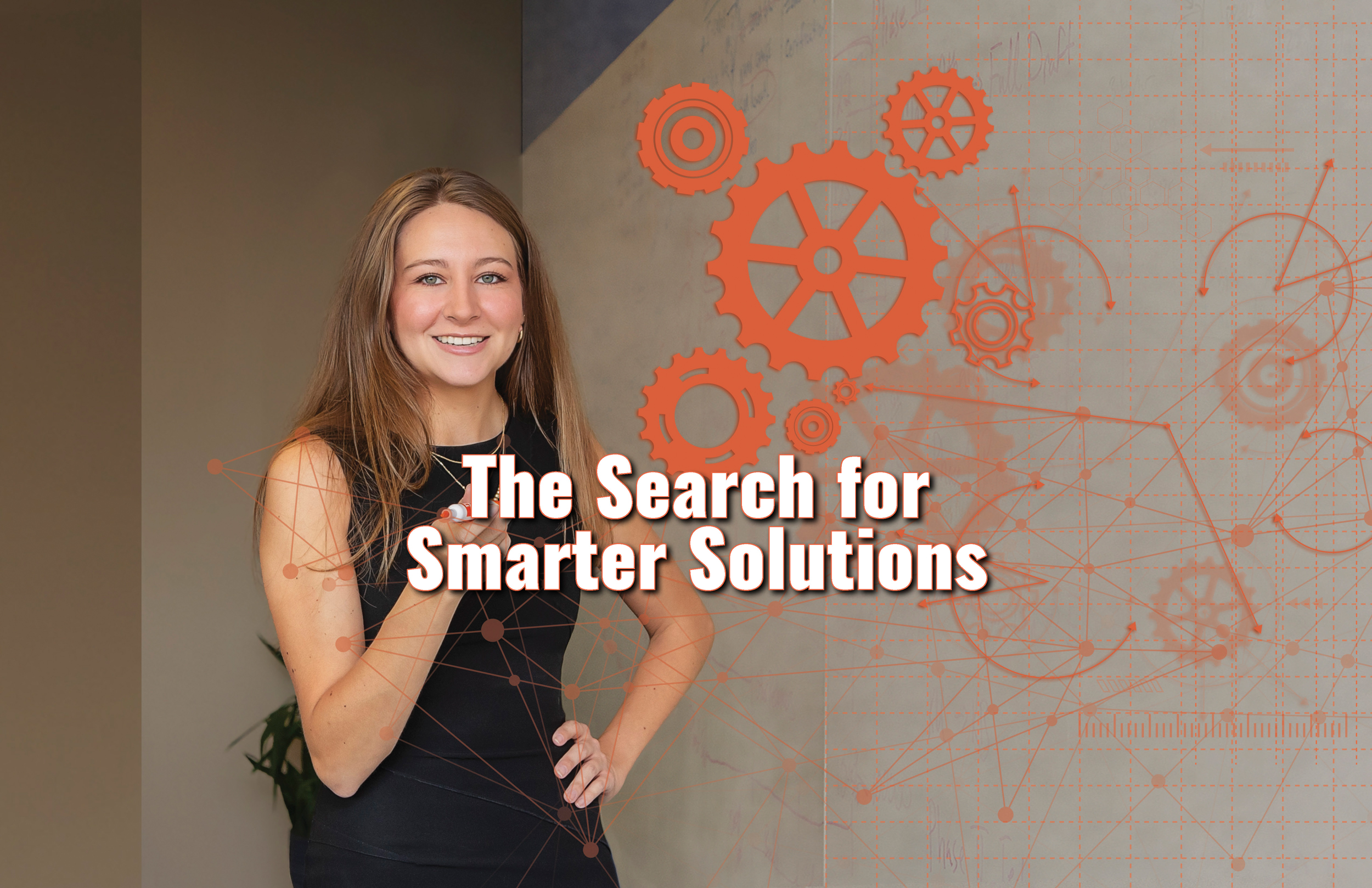
Kalin Baca, PhD, MBA, Co-Founder, COO Icorium Engineering Company
Science, creativity, business, math, research, technology and innovation are all disciplines that come together at the KU Innovation Park (KUIP). Let’s explore what is happening with three of its pioneering engineering companies.
According to the KU Innovation Park website, its mission is to build a resilient, diverse regional economy by helping to create technology and bioscience businesses through recruitment and growth. KUIP creates high-wage jobs by utilizing its affiliations and embracing the strengths and support of the University of Kansas.
One benefit of living in a university town such as Lawrence is there are many opportunities that wouldn’t be available otherwise. The University of Kansas (KU) is designated as a research university, allowing its students and staff to conduct research in a variety of fields. This creates an environment with the potential for new discoveries, innovations and inventions.
Axioforce
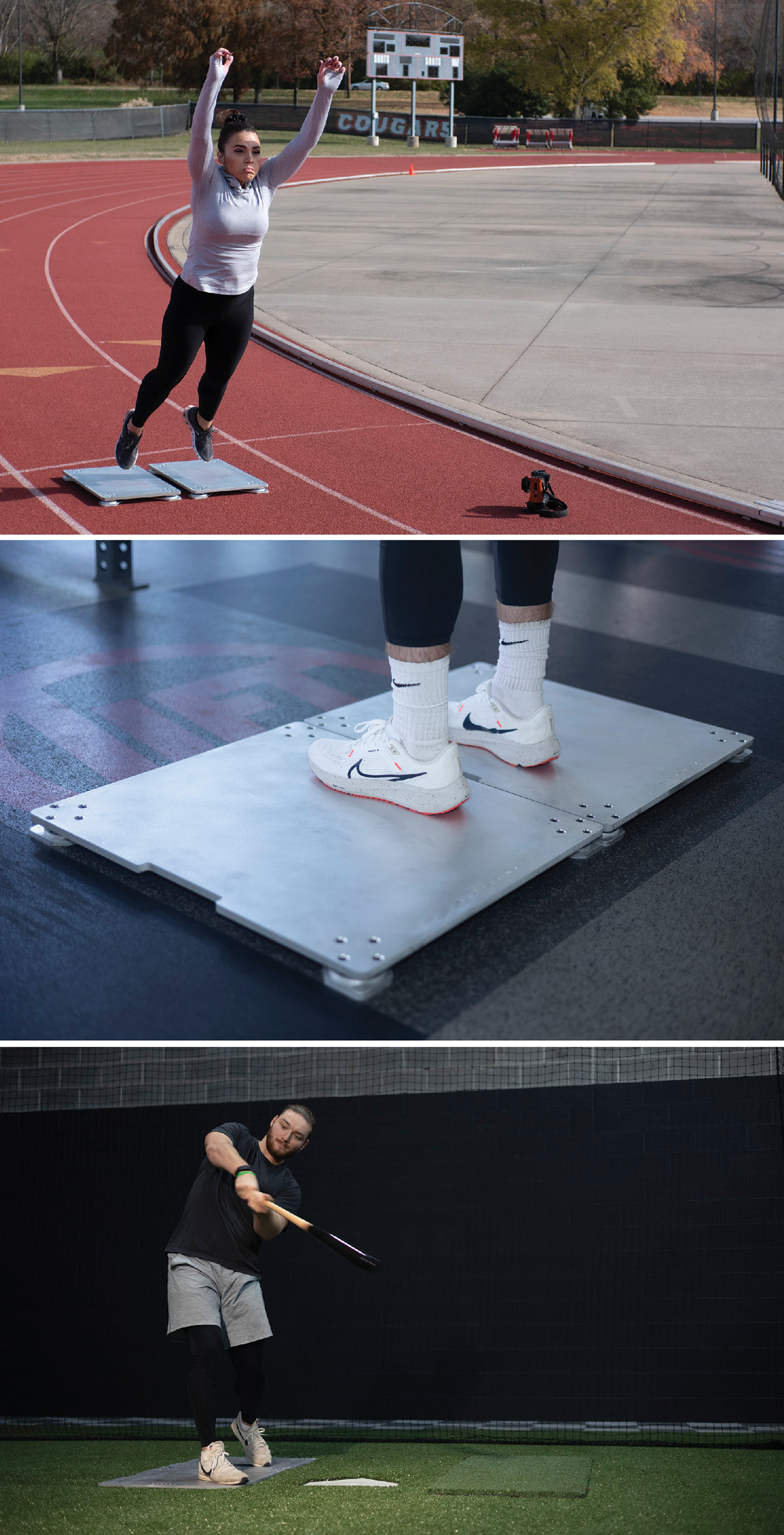
Various photos from AxioForce
Such is the case with Axioforce. Co-founder Jonathan D. Miller, Ph.D., who has his doctorate in exercise physiology, explains: “Our company … is a spinout from technology invented at KU, and now we lease space from KU Innovation Park. We are also exploring different opportunities for seeking nondilutive funding for our company through KUIP or with the help of KUIP.”
Miller says the company has “developed a new kind of smart material that allows us to build things like smart shoe insoles for gait monitoring or smart padding that can detect impacts on sensitive equipment.” The smart material is a magnetic-silicone composite that functions as a 3D force sensor. It is soft, small, lightweight and more cost-effective than typical 3D force sensors, he says.
The technology has applications in many different industries, including one industry near and dear to many Lawrencian’s hearts: sports. Using this unique technology—3D force plates, one of the main tech used by the sports field now—allows the measuring and analytics of an athlete’s performance and training loads, Miller continues. It is a huge trend right now in sports to integrate different technologies into training and practice. The data provided by these tools can help coaches and, in turn, athletes to have less fatigue, lower risk for injury and better performance.
In addition, Axioforce is developing a smart shoe insole that its team believes “will have extremely important implications for athlete monitoring,” he adds, “by monitoring athletes’ movements through the smart insole with weight, pressure and heat sensors, and then using math calculations to look for opportunities to help limit potential injuries.” This magnetic silicone technology opens up potential that could create a huge shift in sports safety and injury-preventative measures.
But Axioforce’s groundbreaking work isn’t always easy sailing. “Commercializing an entirely new technology platform is a difficult endeavor,” Miller says. “Many times, the best practice for science and the best practice for business disagree with one another, and this creates some tension in our work. Finding the best of both worlds can be extremely challenging but also equally rewarding.”
As a scientist, Miller relies on the advice of others who have been around business practices for longer. While it is important to have good science, there is a healthy balance between business and science “so we can end up with products that are quality, simple and reliable,” he says.
The mission of developing technologies that move the world forward in a positive way is what drives the engineers and scientists at Axioforce. It brings conviction to what they are doing, Miller explains, as the “long-term goal is to develop technologies like our smart shoe insoles that become a critical piece of preventative health care and help millions of people avoid premature disability and disease.”
Part of the company’s endeavors is working with military veterans who have had an amputation using silicone-based sensors with an interface between the removed limb and the prosthetic. A large percentage of veteran amputees have diabetes, Miller explains, a common cause of which is neuropathy. This can lead to a loss of nervous functions including feeling, as well as immune issues, infections and limitations to the body’s ability to heal itself. It can cause a greater risk for additional issues within the limbs that lead to a higher possibility for additional amputation.
Much like with the athlete, Axioforce technology, when applied in veterans’ prosthetics, can provide data that can help to warn and mitigate issues before they become a problem, potentially helping reduce the need for additional amputations and more harm to the veteran.
Icorium Engineering Co.
Kalin Baca, Ph.D., co-founder and COO of an engineering spin-out from the University of Kansas, along with co-founder, Mark Shiflett, have been connected to the KU Innovation Park since before their company, Icorium Engineering Co., began. The company has utilized the park’s resources as a “virtual tenant, an accelerator suite tenant and now full tenant. The park has been extremely supportive and a great resource for us,” Baca says.
LOCAL MATTERS
Our Local Advertisers – Making a Positive Impact
Icorium is focused on developing new technologies to separate azeotropic refrigerant mixtures (complex refrigerant mixtures that are difficult to separate) into their original component materials, which allows them to be recycled, she continues. The first commercial refrigerants used chlorofluorocarbons (CFCs), which were found to be a major contributor to ozone depletion and were phased out of production. New refrigerant blends were created using hydrofluorocarbons (HFCs), which have zero ozone depletion, but were found to have extremely high global warming potential that contributes significantly to global warming. Because of this, many HFC refrigerants, such as those commonly used in home air-conditioning units, are being phased out.
“The refrigerant industry is currently going through a legislative-driven phasedown of the production of the refrigerants that are used today (HFC blends),” Baca explains. “As this phasedown continues, and we transition to the new hydrofluoroolefin (HFO) refrigerant blends, there will be a need for recycled refrigerant to service existing equipment and to use recycled refrigerant in new equipment.”
When refrigerants are recovered from a system, they have the potential to be reclaimed and recycled. “The azeotropic mixtures were designed so that if a leak occurs, the mixture does not lose one component preferentially,” she adds. “This is helpful for use, but at end of life, the azeotropes make it very difficult to efficiently bring a mixture back into spec or separate the mixture into individual components.” In turn, many of the recovered refrigerants must be stored en masse or destroyed. Icorium is developing better ways to recycle and eventually repurpose them.
Using technology and through research and testing, Icorium has found a way to take something considered waste and repurpose it, Baca says. “We have the ability to help create circular economies for critical materials and have a substantial environmental impact by turning what is often considered waste into a valuable material that can be recycled.”
The Icorium website explains: “Our mission is to address complex environmental challenges and mitigate global warming through sustainable engineering. We develop and transform novel technologies into commercial solutions for separating and recycling complex chemical mixtures.” The company is committed to pioneering sustainable engineering practices that redefine industries and leveraging technology to solve complex environmental challenges.
In addition to solving environmental challenges, “Startup company funding is always a challenge; we have been supported by nondilutive grant funding from the National Science Foundation thus far and are now looking at starting a seed round,” Baca explains. Icorium originally started with funding from a grant, and with Phase 1 of funding complete, the company is continuing to expand funding into Phase 2. “We are operating a pilot scale extractive distillation process and are starting work on a commercial demo plant,” she adds.
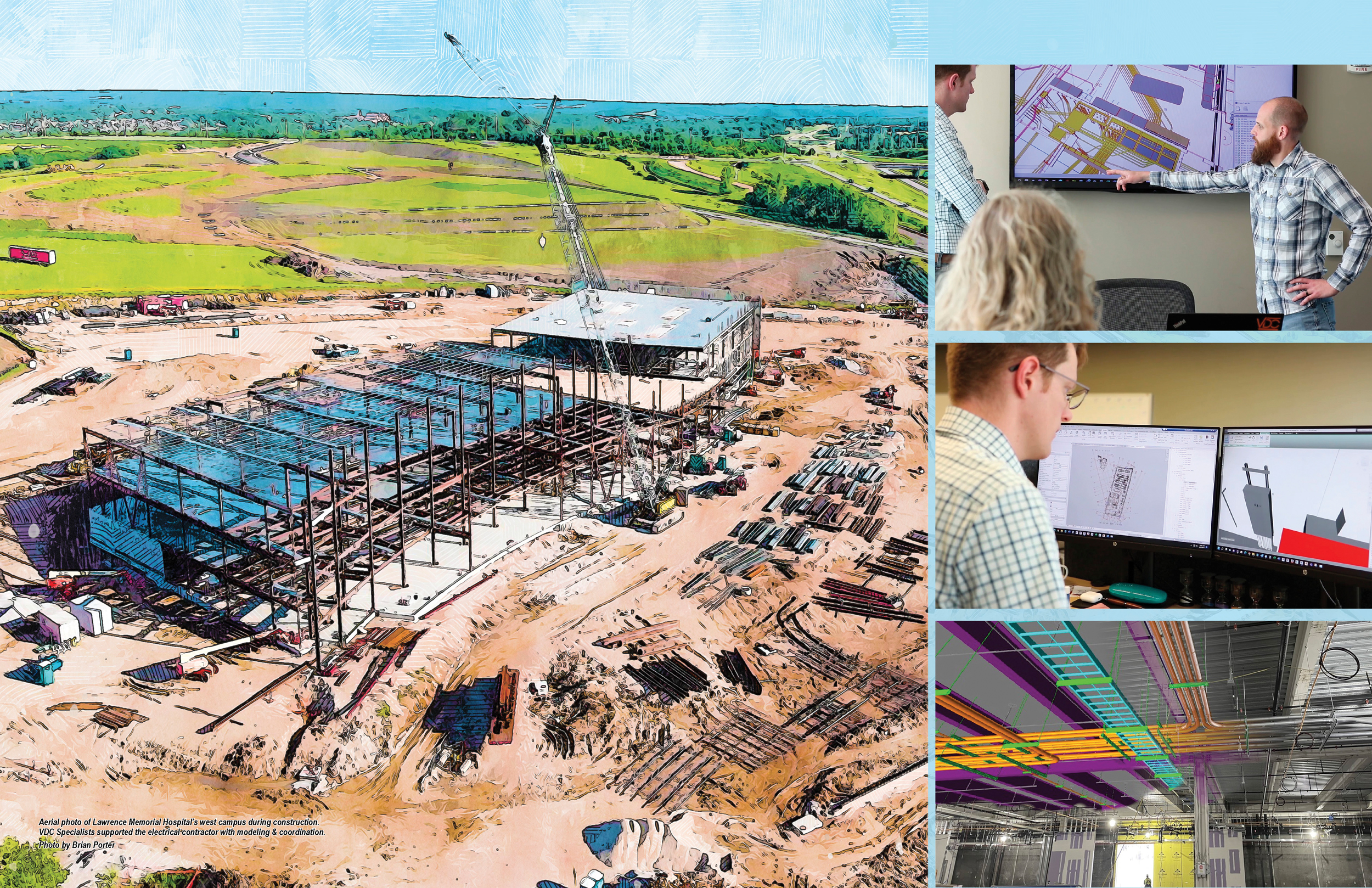
Background: Aerial photo of Lawrence Memorial Hospital’s west campus during construction. VDC Specialists supported the electrical contractor with modeling & coordination.
Right: Michael Munson (right) and Heath Robertson (left) discuss layout options for an electrical room at a large corporate campus in Bentonville, AR;
Heath Robertson working to model and coordinate complex electrical systems on a commercial office building;
Photo displaying the level precision with which VDC Specialists models and plans for construction by blending an image from the jobsite, overlayed with an image from VDC Specialists’ model in the same location on a large data center near Atlanta, GA.
Photos by Brian Porter.
VDC Specialists
In 2018, Heath Robertson, president and founder of VDC Specialists, started a business in the spare bedroom of his duplex and soon after became a tenant at KU Innovation Park. While VDC Specialists isn’t an engineering company itself, he says, it works with MEP (mechanical, electrical and plumbing) design engineers, electricians, architects and contractors nationwide to execute BIM (building information modeling) coordination, virtual 3D models that fill the gaps between what engineers put in drawings versus what actually happens in the field, enabling offsite prefabrication and better project planning.
“Taking what the engineering and architectural teams show on their drawings, we break it down to minute levels of detail to figure out how the system will be installed as a whole rather than just where end devices will go,” he explains. “After our process is completed, we’re able to generate sheets that allow the electrical contractors on the project to prefabricate large portions of the systems offsite, allowing the projects to be completed more efficiently and with less surprises throughout the construction process, since the system gets installed in large assemblies rather than in thousands of individual components.”
Robertson says after the models are created, it is very similar to a large-scale Lego process for contractors. It helps take the guesswork out of ordering materials, which allows for better procurement and communication, and less overall time to build the project.
How does a small company that started around six years ago in an extra bedroom in Lawrence, Kansas, go from startup to working on some of multiple Fortune 100 companies’ largest projects? “We are proud to have worked on major projects spanning the entire country, from high-profile projects including battery plants, corporate headquarters, multimillion-square-foot data centers, international airports, hospitals, research laboratories and NFL stadiums—all totaling over 30 million square feet,” he says.
Working with another company earlier on that provided similar applications in Topeka, Robertson saw more opportunities that could be tapped. With the new business, he began to build “great partnerships that … ultimately lead to these project gains that continue to fuel growth.” He says it’s rewarding working hand in hand with field teams that install electrical systems to make sure VDC Specialists’ coordinated models are able to be constructed and installed just as they model it, then seeing large, prefabricated assemblies being lifted into the air and put into their final place without issue.
And he is proud to have the company headquarters in KU Innovation Park. “It’s a truly unique place with a staff that is unparalleled in their willingness to ensure you have the tools you need to be successful,” Robertson adds.
VDC Specialists looked for ways to give back and drive growth and development for the construction industry around Northeast Kansas. This year, the company partnered with Washburn Institute of Technology to financially support 24 students in attending Skills USA, as well as provided the opportunity for all 18 graduating electrical students at Pittsburg State University to take their journeyman licensing exams.
Robinson believes the work his company has done with the virtual construction process and “its proven efficiency gains and construction optimization,” the demand will continue to increase each year. He says other technologies, such as AI, “will absolutely be playing a role in the next five to 10 years, but I see that as an excellent opportunity to further streamline our processes and to eliminate even more of the repetitive tasks that we continually automate through traditional programming methods. It’s ultimately something that I welcome with open arms.”
For technical and college students, or others interested in similar work, Robinson reminds them that “it is important to focus on process and workflows rather than specific programs … The next program is always right around the corner, so understanding the end result of what you’re doing in the program is vital to your longevity in any field.”