story by | |
photos by | Steven Hertzog |
OPEN A PDF OF THE ARTICLE |
When choosing a home base for a manufacturing business, the positives far outweigh the negatives here in Douglas County.
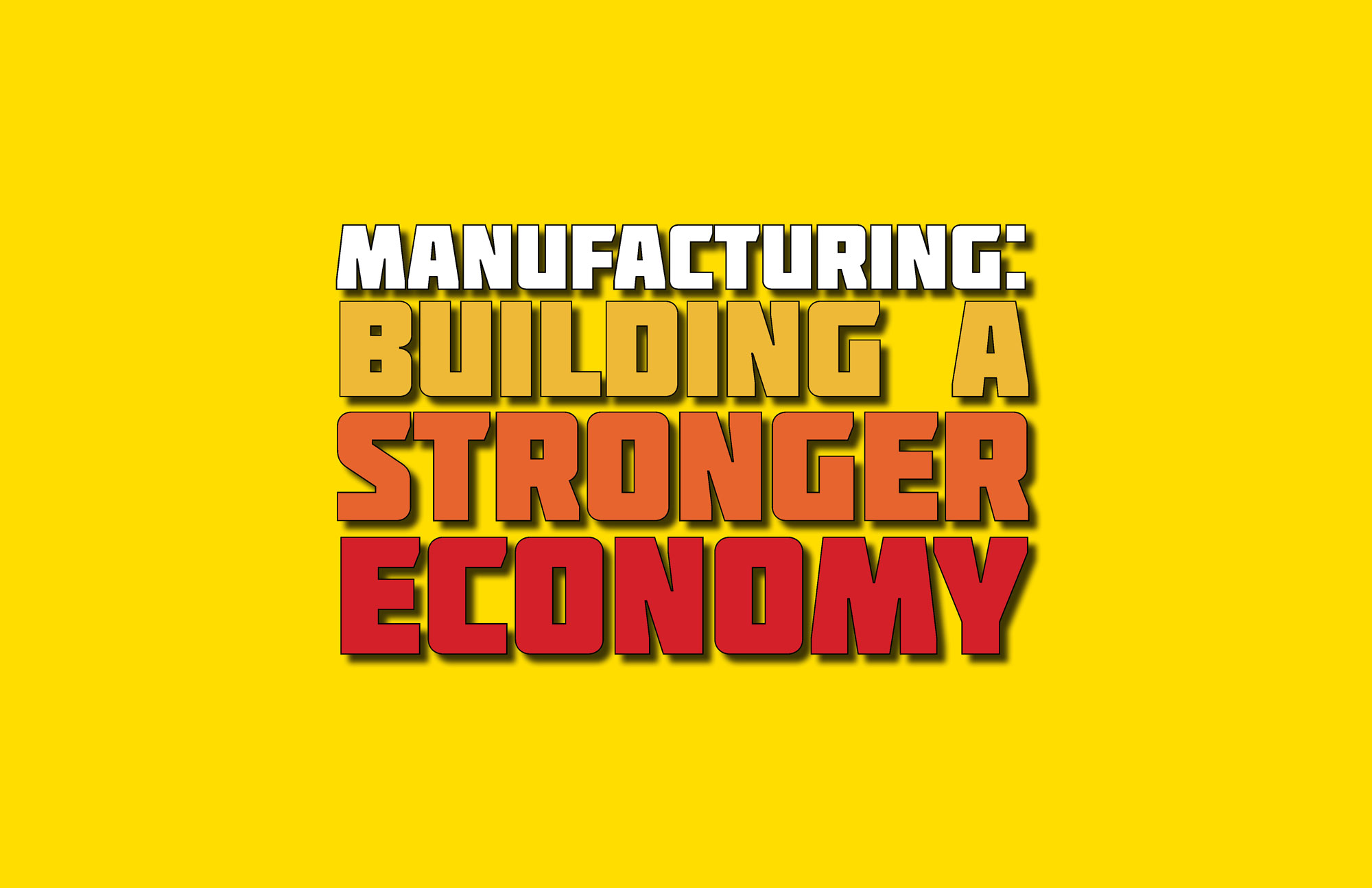
Manufacturing Adds to Local Economy
Brushed concrete floors, glossy and sparkling clean.
Immaculate stainless steel surfaces.
LED numbers displayed in red and green on electronic gauges.
The whir of air purifiers overhead.
Is it a hospital? A commercial kitchen? No, it’s a typical modern manufacturing facility.
Gone are the days that most manufacturing jobs entail dusty, grimy workplaces. Now, when you enter a manufacturing business, you are more likely to see pristine machinery and high-tech robotics—even in the simplest of operations. This isn’t your grandparents’ industry anymore.
“We’ve struggled against the perception of manufacturing as dirty and repetitive. This isn’t ‘Laverne & Shirley.’ These are highly technical, clean environments, because so much of manufacturing is automated,” says Tiffany Stovall, president and CEO of Kansas Manufacturing Solutions.
Believe it or not, Kansas ranks 12th in the nation for the percentage of gross domestic product (GDP) from manufacturing, according to the U.S. Bureau of Economic Analysis and Kansas Manufacturing Solutions 2021 annual report. There are almost 174,000 manufacturing jobs in Kansas, including about 5,000 in Douglas County, according to the same report. The average manufacturing job in Kansas pays $59,650 per year, much above the average non-manufacturing salary of $48,000 to $49,000 per year, Stovall says.
Most of Kansas’ manufacturing jobs are centered in metropolitan areas, and Douglas County would not typically qualify as its own metropolitan area. Yet, we are home to many longtime, successful manufacturing operations, and we add more every year.
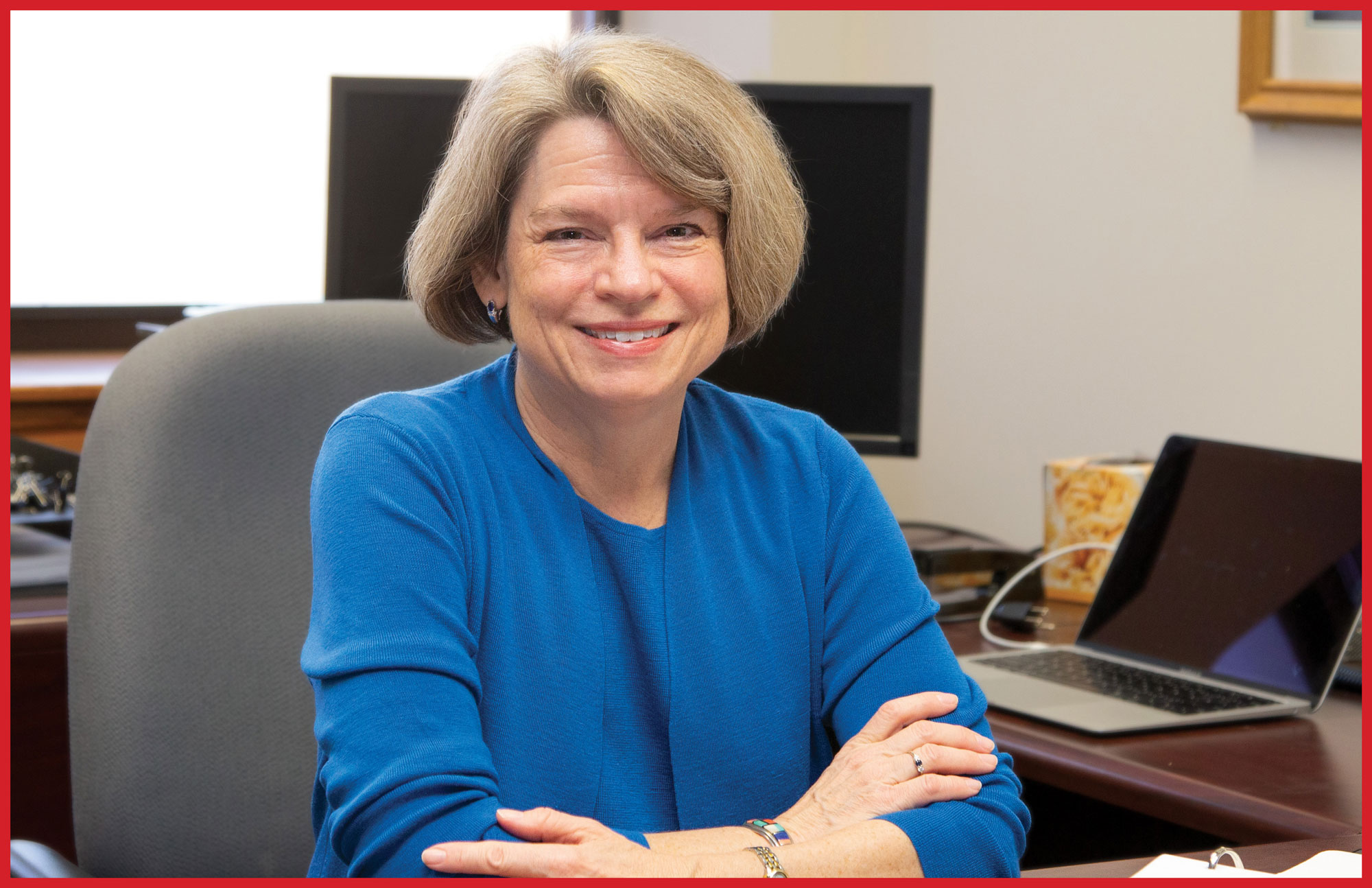
Economist Donna Ginther, Director of the Institute for Policy & Social Research
“Douglas County is a company town, as in the University, which has an outsize impact on our industrial mix,” says Donna Ginther, professor of economics and director of the Institute for Policy and Social Research at the University of Kansas (KU).
Ginther says manufacturing in Kansas accounts for about 16 percent of the state’s GDP, while manufacturing is about 11 percent of Douglas County’s GDP; KU and government are about 25 percent of Douglas County’s GDP.
So the county is below the state’s average for manufacturing revenue, but that in no way means that manufacturing in Douglas County is below average in any other sense.
As many large and small local manufacturers can attest, Douglas County has attributes that make it appealing and provide advantages to manufacturing businesses. And many of those characteristics set Douglas County apart from other locations in Kansas.
Of course, the county also has a few challenges with which manufacturers must contend. Many of those challenges, such as workforce shortages and supply-chain issues, are affecting manufacturers statewide—and nationwide. However, if recent establishments and growth are any indication, the positives of this location greatly outweigh the negatives.
Intermodal Transportation Is Key
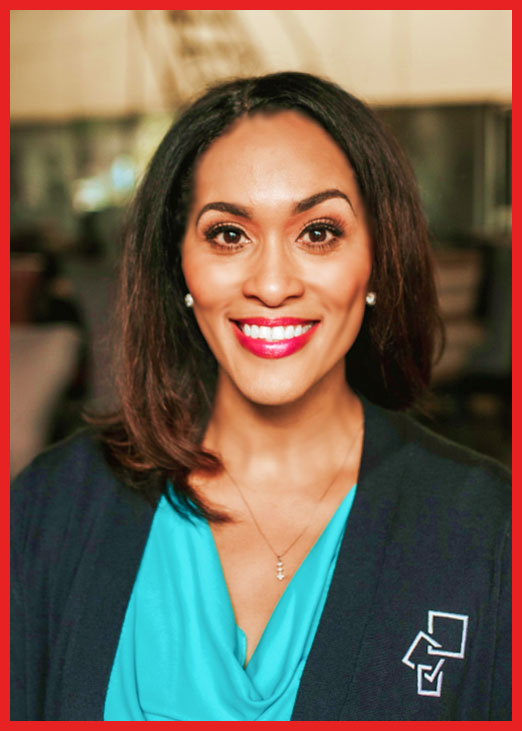
Tiffany Stovall, CEO Kansas Manufacturing Solutions
Traditionally, manufacturing in Kansas has comprised two main categories: aviation and agriculture processing. Those industries both continue to thrive statewide, but they are not the thrust of manufacturing in northeast Kansas or in Douglas County.
“We also have a lot of manufacturing in chemicals, food manufacturers and processors, and transportation equipment in Kansas. We have trailer manufacturers and a lot of places that make specific pieces and parts for cars and buses,” Stovall says.
Ginther points to Garmin, a manufacturer of GPS, as an example of a high-tech manufacturer that chose to locate in northeast Kansas.
Most of those operations predate what was a seminal establishment in northeast Kansas in 2015 and is having a large impact on manufacturers in Douglas County, as well: the Logistics Park Kansas City Intermodal Facility in Gardner-Edgerton, which unifies transportation modes and routes like never before.
“That operation has exploded and has changed our area. We are very close to that; it even encroaches on DeSoto. Lawrence is merging into the outer Kansas City area. That is why you see a lot of development on the east side of town,” says Kate Chinn, franchise owner and CEO of Lawrence Express Employment Professionals.
Stovall says the intermodal facility has tremendously enhanced the appeal of northeast Kansas as a place that manufacturers want to locate.
“We already had a central location. Now we are at the crossroads of interstates and an intermodal hub, which includes train or plane, national or international,” she says.
Douglas County Manufacturing
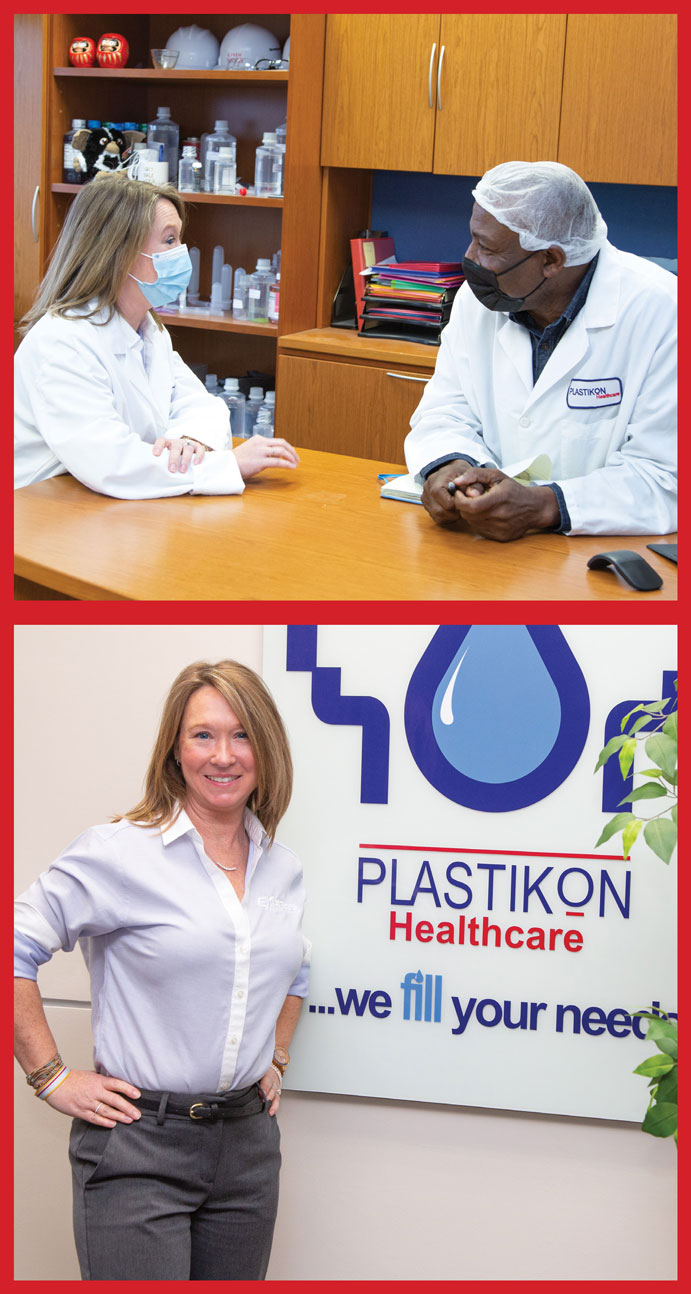
Owner Kate Chin of Lawrence Express Employment Professionals at Plastikon to discuss employment candidates
Lawrence and Eudora are home to two longtime industrial parks, East Hills Business Park and Intech Business Park, respectively, which house many manufacturing operations. A third industrial park, VenturePark, was more recently established on the site of the former Farmland Industries plant in Lawrence and has sites for further potential manufacturing. The Lawrence area is also home to traditional manufacturers such as Lawrence Paper Co., Berry Global and Hallmark Cards.
“We have unique manufacturers here in Douglas County that are not necessarily related to agriculture, even though we grow wheat as a mainstay of our economy in Kansas,” Chinn explains. “We have a medical device company. We have the largest garage door manufacturer in the world. There are amazing companies here.”
Both Chinn and Stovall emphasize that manufacturers need all sorts of workers for many different jobs, not just the people who fill the production lines or warehouse operations. So when a manufacturer chooses to locate in the county, it will seek a workforce that offers a variety of skills.
“You just don’t think about how many different positions manufacturers need at so many levels. I do professional placements for engineers, drafters and finance positions, not just production,” Chinn says.
Stovall’s Kansas Manufacturing Solutions does outreach specifically to inform communities and students of the range of jobs and careers that manufacturers can offer to them.
“Yes, there are shop floors that need people who are welders. Do you like to talk to people? They also need a sales force. They look for talent coming out of universities too, like engineering and accounting,” she says.
Though there are, and likely always will be, many positions and opportunities at the entry level in manufacturing, the operations—just like the rest of the world—are increasingly technical. Manufacturers require a skilled labor force, people who have at least some technical training, to fill positions such as CNC (computer numerical control) machinist, a precision programming ability.
“If you’re going to attract a manufacturer to a county, one of the first things they’ll ask is, ‘What is the skilled workforce, and what are the training supports?’ ” Stovall says.
The Dwayne Peaslee Technical Training Center, aka Peaslee Tech, opened in Lawrence in 2015. Prior to that, other than some high school classes in the trades, Douglas County did not have local training opportunities for a skilled workforce. Peaslee Tech now partners local industry and the school district to provide skilled training and certifications for current and future manufacturing employees. Now there can be a direct pipeline to feed skilled employees to local employers. And local students can now envision themselves in those workplaces with careers that keep them in Douglas County.
“Peaslee Tech offers great promise. That’s where you get your skilled technical workforce,” Ginther says.
Workforce Challenges
The Great Resignation—the nickname given to all of the workforce changes during the COVID-19 pandemic—absolutely has affected manufacturers. However, as Chinn says, manufacturers already were experiencing labor gaps and labor shortages for about 10 years before the pandemic, as baby boomers were retiring, and there were not enough young skilled laborers to replace them.
Local manufacturers have had to increase pay to recruit and retain production staff. Chinn says wages were increasing pre-COVID, and they increased significantly again just in the past year.
“For example, an entry-level production position, say, packaging a product into a box now has a starting wage of about $16 per hour. A few years ago, that same position would have paid $12 to $13 per hour,” she says.
Ginther notes that although the wages have increased dramatically in some instances, it might not always be enough of an increase to keep up with the recent spikes in inflation.
Stovall says employees are feeling more empowered to speak up and ask for what they want. Some are using their collective voices to push for more flexible work scheduling and even changing long-established shift hours of some manufacturers.
“Several manufacturing companies here have changed to Monday through Thursday 12-hour shifts. Then they have a whole other crew that works Friday, Saturday and Sunday. The core staff was getting burned out, and they became aware that people would just up and quit,” Chinn says.
The weekend shifts have a pay differential, and companies have started to pay incentive bonuses for employees after six months and 12 months of employment in order to retain them, she adds.
Stovall says many manufacturers have begun to offer paid time off to hourly employees, something hourly workers do not usually have and was previously unheard of.
Some manufacturing companies also now offer financial counseling and mental health counseling to employees in an attempt to supply more benefits to employees and differentiate themselves, Stovall and Chinn agree.
Future Manufacturing
Ginther says we only need look as far as today’s headlines to see what needs to change in the future of manufacturing. Thanks to the shortages and shipping delays of the past year, the term “supply chain” has made its way into almost every American’s vocabulary.
“Strategically outsourcing production to other countries comes at a cost that we’re paying right now when we can’t get the goods. For the benefit of the economy, we need to rethink manufacturing coming back here to the U.S.,” she says.
Stovall says many companies sent production operations overseas to save money.
“It’s not as cheap overseas now, and if you can’t get your product, it doesn’t matter how cheap it is,” she adds.
Companies and manufacturers will need to focus their attention on building regional and local supply chains, and sourcing locally to avoid these problems in the future, she says.
On the local front, both Ginther and Chinn point to KU’s planned development of Innovation Park to both grow and pull talent from KU in ways that will benefit the local economy, including local manufacturers.
“We need more high-tech spin-offs from the University and other industry. Ames, Iowa, has grown and developed a manufacturing setting with Iowa State University, and possibly we could do something similar at KU,” Ginther says.
Chinn believes a couple of practical matters need to be addressed in Douglas County, particularly for people who work second and third shifts, and weekend hours.
“There is nobody in this town who has third-shift child care, and it’s becoming a huge issue in Douglas County,” she explains.
Ideally, a child-care center should be located near businesses so parents can easily drop off and pick up their child before or after work, Chinn says. There are conversations taking place in town and with The Chamber to work toward solutions.
The other challenge is that city-run public transportation does not operate 24 hours per day. So workers may only have bus transport either going to or coming home from work. If they do not have a car, they either have to rely on others or pay for private transportation, neither of which is a sustainable solution, she adds.
Ginther says the opportunity for growth in manufacturing in Douglas County is good for everyone who lives here.
“Having good jobs for all residents is paramount, and we could really benefit from having more jobs here as opposed to commuting to Topeka and Johnson County,” she says.