Music to Our Ears
Complex and time-consuming to make, Reuter Organs are made right here in Lawrence.
| 2017 Q2 | story and photos by Steven Hertzog
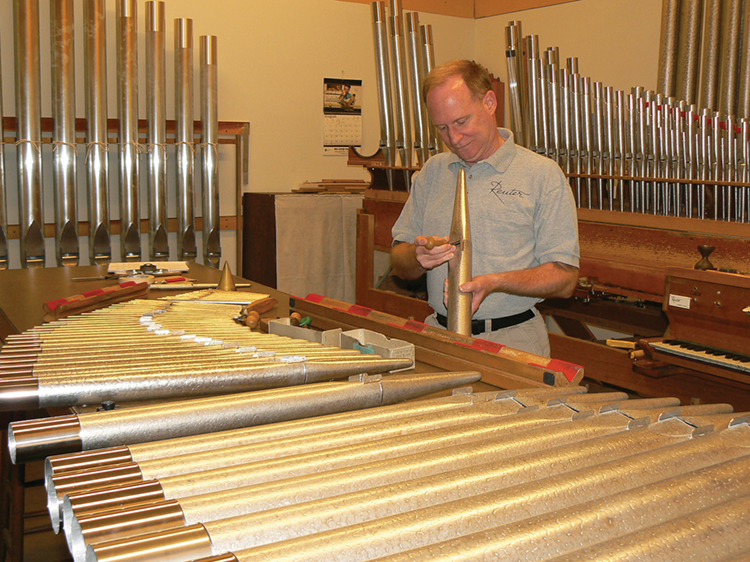
New pipes receiving their initial shop voicing
Complex and time-consuming to make, Reuter Organs are made right here in Lawrence.
When someone thinks of the great violins of the world, one thinks of Stradivarius and the city of Cremona, Italy. When someone listens to the finest pianos in the world, one is often hearing a Steinway, built in New York.
When a guitar maestro is on stage, there’s a good chance the instrument is a Martin, made in Nazareth, Pennsylvania. And when someone is sitting in church anywhere in the United States, odds are they are listening to a Reuter pipe organ, made right here in Lawrence, Kansas.
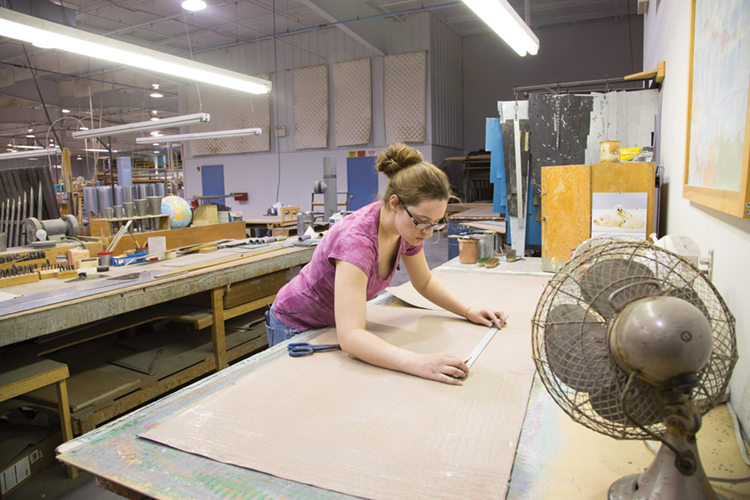
(Top to Bottom) Laying out pipes to be cut and formed ; Freshly formed and soldered pipes before washing; Wiring windchest components; Aluminum-clad expression shades for volume control
In 1919, when an organ was commissioned for the Masonic Temple, in Lawrence, local business leaders put together a package of economic incentives, and the Reuter Organ Co. moved its operation to Lawrence.
The downtown Lawrence building the company moved into, which previously housed the Wilder Brothers Shirt Factory, was located near Sixth and New Hampshire streets. Reuter remained downtown until 2001, when it moved to larger facilities in northwest Lawrence.
The move to larger headquarters allowed the company to cultivate a custom-production line and create a better space to build world-class pipe organs.
As Reuter begins its second century of crafting fine pipe organs, the stewardship now falls under the watchful eye of Albert Neutel, affectionately know to everyone as J.R., (as in J.R. Ewing). J,R. began working with Reuter in the 1980s. He worked as an organ finisher and also handled sales. He took over for his father, Albert, who is now chairman of the board, while Neutel serves as president and chief executive officer.
“First, you start with the sales person,” Neutel says. “Then you go to the engineer, then the pipe makers, the chest makers, the wind systems, the consoles, the voicing; so there are a lot of different facets to building a pipe organ.”
Reuter is a multimillion-dollar international firm with organs in the United States, Canada, Taiwan and Korea. There are very few pipe organs in the Asian market right now, and Neutel is working to change that. He spends as many as 250 days a year traveling the world promoting the Reuter brand. Besides churches and synagogues, people will put pipe organs in concert halls, universities and even private residences.
The creation and manufacturing of a Reuter pipe organ is incredibly labor-intensive. Neutel estimates that more than 1,000 hours of labor go into the making of a single custom-made organ. Think about it: If one person worked full-time to build an organ, it would take nearly six months to complete.
The cost of a pipe organ makes it a high-end luxury product. Next to the construction of a church, its pipe organ is likely the second-most costly part of the church. A modest, brand-new pipe organ in today’s economy would cost anywhere from $350,000 to several million dollars.
What makes each pipe organ so unique is mainly the space in which it is installed, the acoustics and the visual setting.
“We have a saying in the organ business that if an organ looks good, it automatically sounds good, at least to the public,” Neutel says. “And that’s eight-tenths of the battle. But there are so many organs you don’t see because they are built behind screens, so then that organ gets evaluated only on what people hear.”
It’s a fact that 99 percent of all Reuter organs are built in Lawrence. Reuter brings in raw metal for its engineers to melt down and shape into the company’s proprietary pipes. The company brings in its own wood to build wood pipes, wind chests and structural framing. Reuter builds its own keyboards and some of the electrical components. The company handles its own engineering, milling, casting and pipe-making. It also makes its own wind chests, consoles and casework, and does its own finishing, assembly and installation.
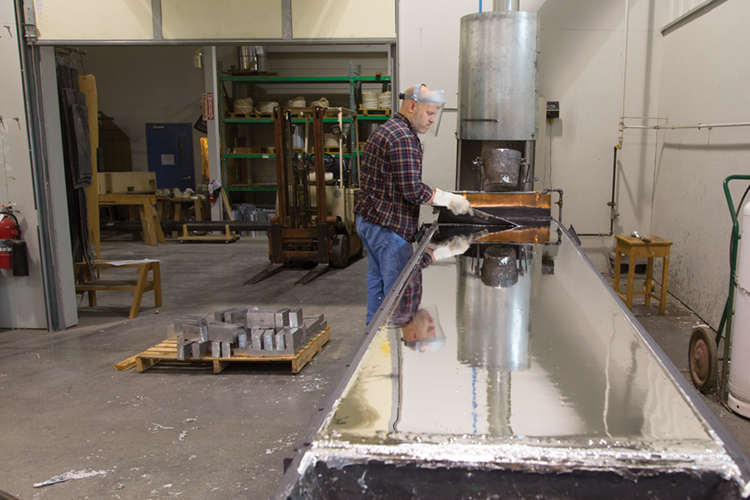
Casting sheets of pipe metal.
Perhaps one of the most fascinating and least-known elements of creating a pipe organ is “voicing” the pipes. Reuter has a team of voicers that literally gives voice to the pipes, which, in effect, is teaching the pipes to sing. The members of the company’s voicing team are all professional musicians. They prepare every pipe for every organ and produce balanced ensemble sound with consistent speech and tone.
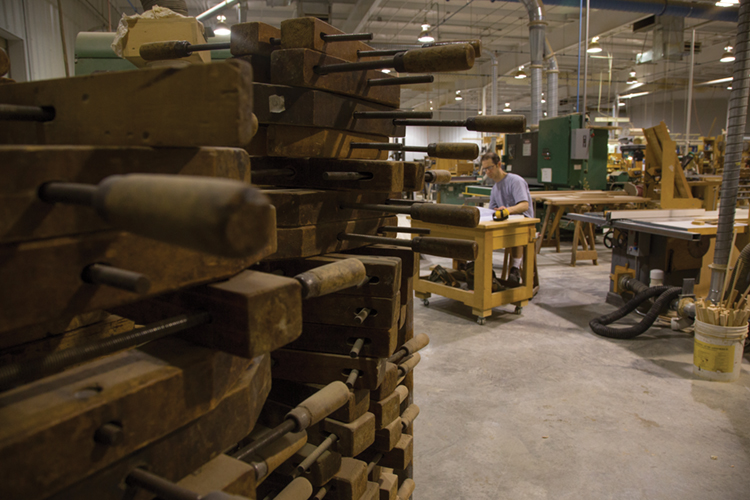
At work in the case department.
Music enthusiasts refer to Nashville as the home of country music. Memphis is the sound of rhythm and blues. New Orleans gave birth to jazz.
Antonio Stradivari created the finest violins the world has ever known. The early mass production of rock ’n’ roll can be attributed to the Tin Pan Alley. Soul music was derived from African American gospel music being sung in Southern churches. And thanks to Reuter, the city of Lawrence, Kansas, may just be the home of the church pipe organ.
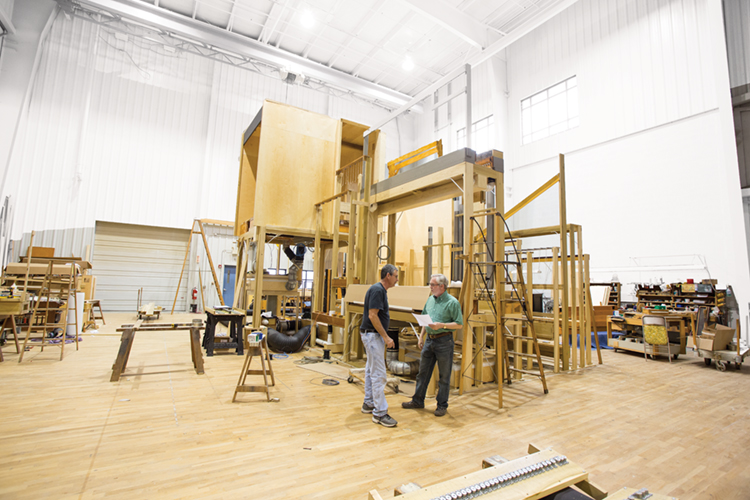
Construction progressing in the assembly room.
84 Comments
We stumbled over here by a different website and thought I should check things out. I like what I see so now i’m following you. Look forward to checking out your web page again.
Next time I read a blog, I hope that it won’t disappoint me just as much as this particular one. I mean, I know it was my choice to read, but I actually believed you’d have something helpful to say. All I hear is a bunch of complaining about something that you could fix if you weren’t too busy searching for attention.
Very good blog post.Really looking forward to read more. Cool.
Thanks for the article, can I set it up so I get an update sent in an email when you make a fresh post?
Very nice post. I absolutely appreciate this site. Stick with it!|
I used to be able to find good information from your content.
Amazing! This blog looks just like my old one! It’s on a totally different subject but it has pretty much the same page layout and design. Great choice of colors!
Hi, I do believe this is an excellent site. I stumbledupon it 😉 I’m going to revisit yet again since I saved as a favorite it. Money and freedom is the greatest way to change, may you be rich and continue to help others.
There’s certainly a lot to find out about this topic.I really like all of the points you have made.
Excellent article. I am dealing with some of these issues as well..|
Usually I do not read article on blogs, but I wish to say that this write-up very forced me to try and do so! Your writing style has been surprised me. Thanks, quite nice post.
I cannot thank you enough for the blog.Really looking forward to read more. Really Cool.
I would like to thank you for the efforts you’ve put in writing this website. I am hoping to view the same high-grade blog posts from you later on as well. In truth, your creative writing abilities has encouraged me to get my own, personal website now 😉
It’s actually a nice and helpful piece of information. I am happy that you simply shared this helpful info with us. Please keep us up to date like this. Thank you for sharing.
I really like it when individuals come together and share thoughts. Great website, continue the good work!
I really love your blog.. Very nice colors & theme. Did you create this amazing site yourself? Please reply back as I’m hoping to create my own personal blog and want to learn where you got this from or what the theme is called. Thank you!
A motivating discussion is worth comment. There’s no doubt that that you should write more on this topic, it might not be a taboo matter but typically people don’t discuss such subjects. To the next! Cheers.
Thanks for the auspicious writeup. It in truth used to be a amusement account it. Look complex to more added agreeable from you! However, how can we communicate?|
Having read this I thought it was really informative. I appreciate you spending some time and effort to put this content together. I once again find myself spending a lot of time both reading and commenting. But so what, it was still worth it.
I like it when people get together and share views. Great website, continue the good work.
over the counter ed pills that work – medications for ed causes of erectile dysfunction
Hi there, just became alert to your blog through Google, and found that it is truly informative. I am gonna watch out for brussels. I will appreciate if you continue this in future. Many people will be benefited from your writing. Cheers!
I have mastered some considerations through your site post. One other stuff I would like to talk about is that there are various games on the market designed particularly for toddler age children. They contain pattern recognition, colors, dogs, and styles. These commonly focus on familiarization as opposed to memorization. This will keep children engaged without experiencing like they are studying. Thanks
My family always say that I am killing my time here at net, exceptI know I am getting know-how every day by reading thes nice articles or reviews.
Loved this!
Great post!
Awesome insights!
Great post!
Well written!
I value the blog post.Much thanks again. Fantastic.Loading…
Viagra
Viagra
Porn site
Buy Drugs
Pretty section of content. I just stumbled upon your site and in accession capital to assert that I acquire in fact enjoyed account your blog posts. Anyway I?ll be subscribing to your feeds and even I achievement you access consistently quickly.
Exactly what I needed.
You explained it well.
Sex
I have noticed that over the course of constructing a relationship with real estate entrepreneurs, you’ll be able to come to understand that, in each and every real estate financial transaction, a commission is paid. Ultimately, FSBO sellers never “save” the payment. Rather, they fight to earn the commission by simply doing an agent’s job. In the process, they commit their money in addition to time to conduct, as best they can, the tasks of an realtor. Those duties include exposing the home via marketing, showing the home to all buyers, constructing a sense of buyer emergency in order to prompt an offer, booking home inspections, managing qualification assessments with the bank, supervising maintenance tasks, and facilitating the closing of the deal.
I’m saving this one!
Thanks, great advice!
Thanks for the suggestions you reveal through this web site. In addition, several young women who seem to become pregnant tend not to even seek to get health care insurance because they fear they won’t qualify. Although a lot of states at this point require that insurers give coverage irrespective of the pre-existing conditions. Costs on these kind of guaranteed plans are usually higher, but when thinking about the high cost of health care it may be a safer way to go to protect your financial potential.
Short and sweet, nice!
hey there and thank you for your information – I have definitely picked up anything new from right here.
I did however expertise some technical points using this website, as
I experienced to reload the site lots of times previous to I could get it to load properly.
I had been wondering if your web host is OK?
Not that I am complaining, but slow loading instances times will sometimes affect
your placement in google and can damage your high quality score if
advertising and marketing with Adwords. Well I am adding this RSS to my e-mail and can look out for a lot more of your respective intriguing content.
Ensure that you update this again very soon.
Tornado Cash – Best Crypto Platform for Protects Your Crypto in 2025
Tornado Cash – Best Crypto Platform for Protects Your Crypto in 2025
Thanks for the clarity!
Tornado Cash – Best Crypto Platform for Protects Your Crypto in 2025
I used to be suggested this web site through my cousin. I am no longer certain whether or not this publish is written via him as nobody else understand such designated approximately my problem. You are incredible! Thanks!
Hi to every single one, it’s genuinely a good for me to go to see this web site, it contains valuable Information.|
One other issue is that if you are in a scenario where you don’t have a co-signer then you may really want to try to wear out all of your school funding options. You could find many grants or loans and other scholarships that will supply you with money to help you with classes expenses. Thanks alot : ) for the post.
When I initially commented I clicked the “Notify me when new comments are added” checkbox and now each time a comment is added I get three emails with the same comment. Is there any way you can remove me from that service? Thanks!
How to Swap Tokens on ApeSwap: A Complete Guide 2025
Tornado Cash – Best Crypto Platform for Protects Your Crypto in 2025
Tornado Cash – Best Crypto Platform for Protects Your Crypto in 2025
How to Swap Tokens on ApeSwap: A Complete Guide 2025
Tornado Cash – Best Crypto Platform for Protects Your Crypto in 2025
Fantastic info, thanks!
Aw, this was a really nice post. In idea I would like to put in writing like this moreover ? taking time and precise effort to make an excellent article? but what can I say? I procrastinate alot and on no account seem to get one thing done.
Well explained, thanks!
How to Swap Tokens on ApeSwap: A Complete Guide 2025
Solid advice, thanks!
When I initially commented I clicked the “Notify me when new comments are added” checkbox and now each time a comment is added I get three emails with the same comment. Is there any way you can remove me from that service? Thanks a lot!|
One other thing I would like to mention is that in lieu of trying to match all your online degree training on times that you end work (since most people are exhausted when they come home), try to get most of your instructional classes on the saturdays and sundays and only a couple courses on weekdays, even if it means a little time off your saturday and sunday. This is really good because on the saturdays and sundays, you will be much more rested and concentrated on school work. Many thanks for the different suggestions I have discovered from your web site.
It is perfect time to make a few plans for the long run and it’s time to be happy. I’ve read this post and if I may just I desire to suggest you few fascinating things or suggestions. Maybe you can write next articles relating to this article. I want to read more things about it!|
Fantastic site. Plenty of useful info here. I am sending it to some friends ans also sharing in delicious. And certainly, thanks for your sweat!
Totally agree with this.
How to Swap Tokens on ApeSwap: A Complete Guide 2025
Hi, i feel that i noticed you visited my weblog so i got here to ?go back the want?.I am trying to find things to improve my web site!I suppose its good enough to make use of some of your ideas!!
Learned something new!
I don?t even know how I ended up here, but I thought this post was great. I don’t know who you are but definitely you’re going to a famous blogger if you aren’t already 😉 Cheers!
I’ve been exploring for a little bit for any high quality articles or weblog posts in this kind of space . Exploring in Yahoo I finally stumbled upon this web site. Studying this information So i am happy to exhibit that I have an incredibly just right uncanny feeling I discovered exactly what I needed. I such a lot for sure will make sure to don?t overlook this site and provides it a look regularly.|
Howdy! This article couldn’t be written much better! Looking through this article reminds me of my previous roommate! He constantly kept talking about this. I most certainly will forward this information to him. Fairly certain he’s going to have a great read. Many thanks for sharing!
Hi, I do think this is a great web site. I stumbledupon it 😉 I am going to come back yet again since I saved as a favorite it. Money and freedom is the greatest way to change, may you be rich and continue to guide others.
Hi, I think your blog could possibly be having web browser compatibility problems. Whenever I take a look at your site in Safari, it looks fine however when opening in Internet Explorer, it’s got some overlapping issues. I simply wanted to provide you with a quick heads up! Besides that, wonderful website!
F*ckin? amazing things here. I?m very glad to see your post. Thanks a lot and i’m looking forward to contact you. Will you please drop me a mail?
After looking over a number of the blog posts on your web site, I truly appreciate your technique of blogging. I saved it to my bookmark website list and will be checking back soon. Take a look at my web site too and let me know how you feel.
Hi I am so grateful I found your site, I really found you by error, while I was browsing on Yahoo for something else, Regardless I am here now and would just like to say thanks for a tremendous post and a all round exciting blog (I also love the theme/design), I don’t have time to look over it all at the minute but I have bookmarked it and also added your RSS feeds, so when I have time I will be back to read a lot more, Please do keep up the fantastic work.
You’ve made some really good points there. I looked on the web for additional information about the issue and found most people will go along with your views on this site.|
You’ve made some really good points there. I looked on the web to find out more about the issue and found most individuals will go along with your views on this site.
Aw, this was an incredibly nice post. Taking a few minutes and actual effort to make a superb article… but what can I say… I procrastinate a whole lot and never seem to get nearly anything done.
Saved as a favorite, I really like your site!|
Having read this I thought it was very informative. I appreciate you taking the time and effort to put this short article together. I once again find myself spending a significant amount of time both reading and commenting. But so what, it was still worthwhile!
I just added this site to my feed reader, great stuff. Cannot get enough!