story by | |
photos by | Steven Hertzog |
OPEN A PDF OF THE ARTICLE |
Interest in jobs such as welding and carpentry is on an uptick because of job security, the high cost of a college education and the possibility of getting a good-paying job while remaining debt-free.
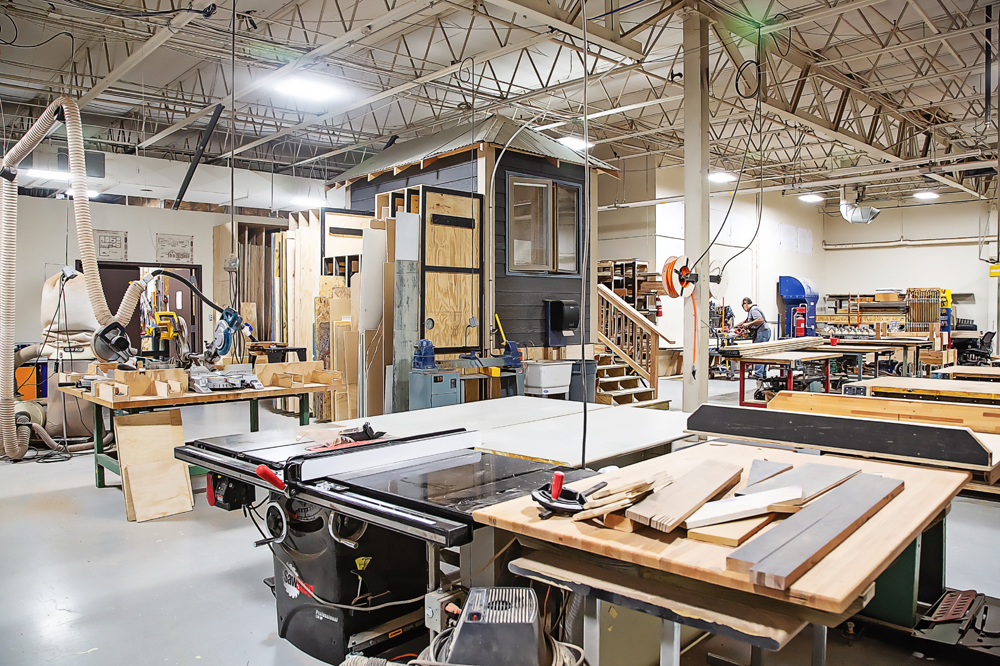
Woodworking and carpentry work studio at Peaslee Tech
At the Dwayne Peaslee Technical Training Center, where Kelley has been CEO the last 5½ years, business is booming. He estimates the training center, best known as simply Peaslee Tech, has 3,000 “duplicated” enrollments (meaning some individuals are enrolled in more than one program) throughout its 31 programs and apprenticeships, which cover everything from the aforementioned welding and carpentry to heating/air conditioning (HVAC), electrician training, robotics and commercial driving. That level, he says, is as high, if not higher, than prepandemic enrollment levels. Many of the training center’s fall classes are already filled.
And interest only seems to be picking up. The high cost of traditional four-year college today and skyrocketing levels of student debt have chipped away at the long-held belief that traditional secondary education is the best way to get ahead and have a prosperous future.
Could it be that trades are the next big thing?
“Since the pandemic, people have realized there are other ways of making a living,” Kelley says. “The thing is, during the pandemic, it was our workers who were essential workers.
“We’ve seen a lot of career changes from the hospitality sector to building trades. The demand is so high for people with skills: pharmacy technicians, medical assistants, court reporters,” he continues. “Electricians, welders, plumbers, HVAC—all are in super-high demand.”
Kelley is quick to point out that Peaslee Tech is not a school but a training center. Because of that distinction, it doesn’t participate in student loan programs. In fact, Kelley says no one gets turned away because they don’t have money to pay for a course, which on average runs around $2,500. Peaslee Tech relies on private donors, government grants and other gift programs to cover costs for students of limited means. Therefore, students can’t leave there with debt.
“The beauty of our model is, we don’t give grades,” Kelley says. “We teach people what they need to know and let outside parties (certification organizations) validate the teaching and learning.”
What Peaslee Tech is doing appears to be working, he adds, as those achieving successful certifications after completing programs is well greater than 90 percent.
Kelley says he has one electronics program that runs four years. In contrast, there is a pharmacy technician program that runs four weeks. Most students work while attending classes. If one is enrolled in an apprenticeship, they’re required to be a full-time employee.
The most popular trade program, by far, Kelley says is the commercial driver’s license (CDL), which provides individuals certification to drive big-rig trucks—18-wheelers. The course consists of 160 hours of training, including 90 behind the wheel. What makes Peaslee Tech’s program special, he adds, is that each student is assigned one instructor and one truck from which to learn. Peaslee Tech has six big rigs available for training.
“Like most of our programs, it’s a performance-based program, so students can complete it in less time if they meet the benchmarks,” he explains.
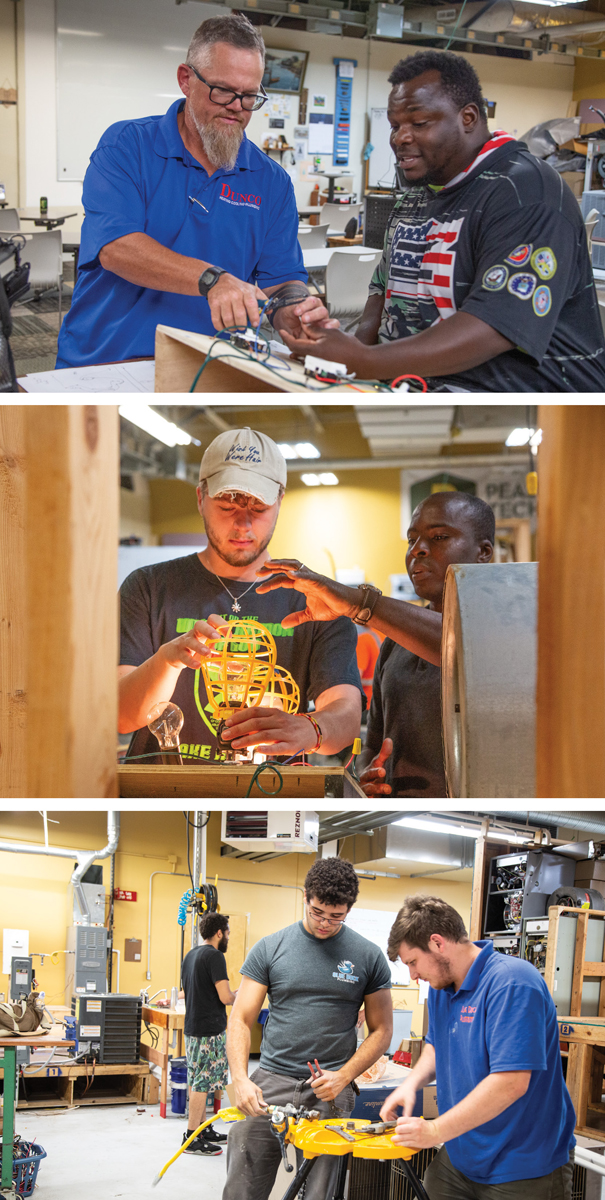
Hands on training for students at Peaslee Tech
Bryson Korir, a native of Kenya, says it took him “about five weeks” to complete his commercial driving license and was all smiles knowing he’d taken an important step in securing a better and more prosperous future for himself and his family.
“I’ve been driving a box truck for two years,” Korir says. “I saw this program (at Peaslee Tech) and saw where I can advance. It’s becoming an in-demand profession. The pay is good. You get to move around while you do your work and get paid.”
He says his dream is to one day own his own truck and operate his own business. And that, Kelley says, is what Peaslee Tech is all about, giving people the needed skills to one day realize their dreams in whatever field or trade they choose.
Along with CDL, some of the most popular trades people are choosing these days include HVAC, welding, carpentry and robotics.
HVAC/Plumbing
Perhaps it’s more than coincidence that an instructor in heating and air-conditioning describes interest in the program as running “hot and cold.” But Riq Quinteros, who’s worked in construction and with machinery most of his adult life, thinks the field in which he teaches could be about to blow up.
“A lot of people of modern generations don’t seem to be mechanically minded,” says Quinteros, who learned to teach trades in a four-year program at Pittsburg State University. “A lot of them don’t understand that there are trades and what different trades do.
“But once they find out, they’re all in,” he adds.
Quinteros says his program consists of 40 weeks, with many nine-hour days—one hour of lecture and the rest lab time, where students take apart and rebuild heating and AC units, learning the ins and outs of the mechanisms.
“They’ll have a completion exercise and then a second-party certification,” he explains. “There are some who come to us who already know a lot and some who don’t.
LOCAL MATTERS
Our Local Advertisers – Making a Positive Impact
“The ones that stick around will be great techs,” Quinteros says.
Eighteen-year-old Chris Howard recently received training in Quinteros’ HVAC class while concurrently honing his skills in his full-time job with Dunco Heating and Cooling. While many of his peers are wondering what to do after high school or sinking money into college, Howard says it’s been nice to be earning good, full-time pay at such a young age.
“At first, I wasn’t into trades,” he says. “I’d always been lazy. But I knew they pay well. Now I love it. I like all the guys I work with. It’s busy, but I’m helping people.”
Much like the automotive tech industry, HVAC and plumbing are trades that constantly are evolving and changing, forcing technicians to constantly learn and adapt.
“Nothing in my class is done for nothing,” Quinteros explains. “Everything is done with a purpose.
“HVAC is not just a job. It’s a way of thinking. But if you take care of the trade, the trade will take care of you,” he says.
Welding
Kelley need only glance at the enrollment trends in Peaslee Tech’s welding courses during the last year to know it is one of the hottest trades in the marketplace.
“We doubled our numbers over the last year in welding,” he says.
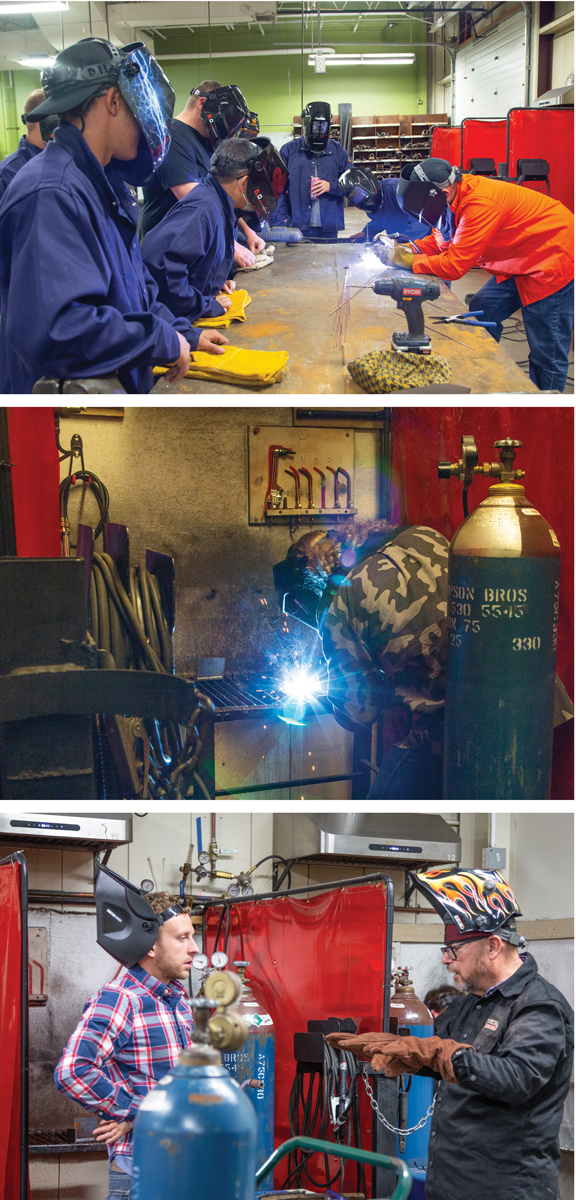
Welding class at Peaslee Tech
David Youmans, who works full-time for a scrap metal company in the Kansas City area and is an adjunct welding instructor at Peaslee, agrees that the current trend in demand for welders is up.
“From what I’ve been told, in the early 1970s, community colleges and trade schools were full,” Youmans says. “Then it started to drop. Schools started pushing more four-year college tracks. While that’s fine for some people, it’s not for everybody.
“Now more people are coming back into it,” he continues. “I work with industrial accounts every day, and every day I hear companies say everybody needs welders. There are a lot of jobs, and a lion’s share pay well.”
Youmans says entry-level salaries for welders typically range from $17 to $22 per hour, while an experienced welder can make $26 to $28. Welders also typically can work a lot of overtime and receive production bonuses.
Peaslee Tech’s beginning welding course runs 14 weeks, meeting for four hours on Tuesday nights. On a recent summer evening, Youmans lectured seven students on topics ranging from LASER (Light, Amplification by Stimulated Emission of Radiation) welding, water pressure welding and push versus pull beads.
“I try not to spend more than 30 minutes at a time in the classroom,” he says, before moving to the shop where students don their protective masks and practice making welding beads. “They’re usually chomping at the bit to arc and spark.”
One of Youmans’ students, Bryce Phillips, grew up on a nearby farm, where he was introduced to welding at a young age.
“I just thought I’d try it out,” says Phillips, who drives a forklift for a local plastics company. “I enjoy it. I’ve definitely learned a lot more about it here.”
Youmans says he’s seen a uptick in interest in welding among women in recent months. He’s had two females in each of his last two terms.
“My dad used to be a welder,” says LeStat Wilson, a student in Youmans’ class this summer. “I’d see him working in his shop when I was about 9. Ever since I saw that, I’ve had an interest in welding. I started welding when I was about 12.
“It’s a good alternative (for a trade), especially when you have family helping and a job helping pay for this,” she adds.
Wilson says it will take her three class terms to complete her training, but she should be ready for a full-time welding job by the end of the year.
“Knowing that I’m more marketable … ,” she says. “It’s a good feeling knowing that a lot of people need welders.”
In fact, Youmans says if welders can’t land a job in the current economy, it’s because they don’t want one.
“This is a great option if you don’t want to go to college or go into debt,” he says. “There are plenty of jobs. If you’re a trained and skilled worker, and not working in this economy, it’s probably because you don’t want to work.”
Manufacturing Automation Systems
It probably should come as no surprise that trends in the job market for anything relating to automation are on the upswing. It only makes sense that, as more and more of people’s daily lives become connected to automation at some level, demand for such services and those who provide them would increase.
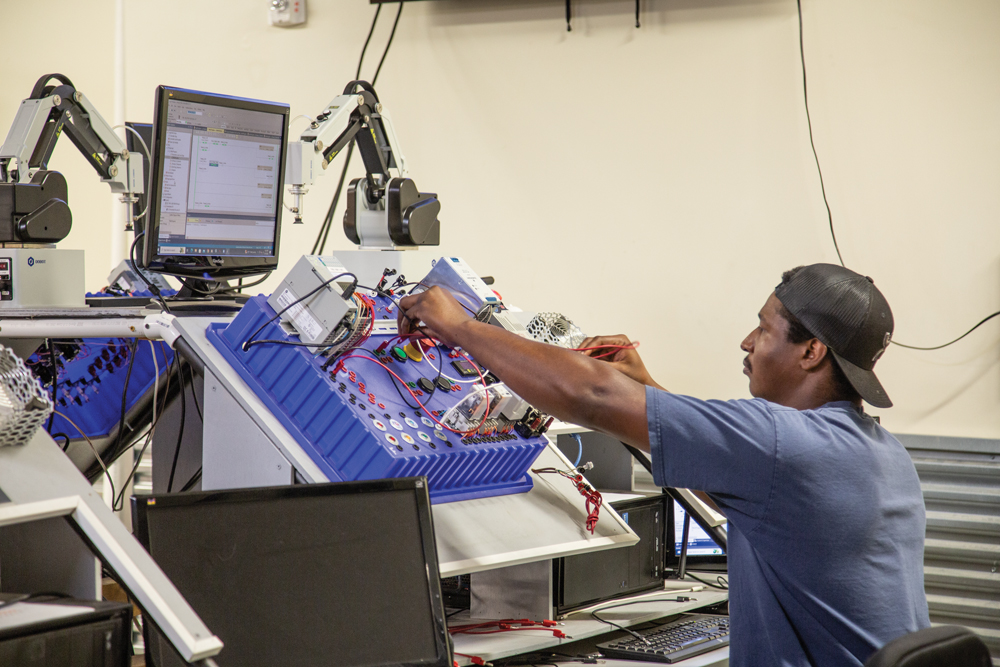
“]“]
Robotics training at Peaslee Tech
Ed Keating, who’s taught the last six-plus years in manufacturing automation systems at Peaslee Tech, has seen this demand skyrocket in recent years. As a result, he says interest in his automation and robotics courses, at Johnson County Community College as well as Peaslee Tech, have increased dramatically, as well.
“Everything is getting more technical,” Keating says. “You need more people to support that.”
He says U.S. manufacturing is on the rise because of political instability in foreign countries, inability to control quality at remote locations and logistic delays, which will lead to increases in employment. At the same time, manufacturing here is growing more complex, driven by the need for real-time production data (inventory management, maintenance management), the need to coordinate real-time scheduling across multiple manufacturing plants and the need to integrate data from the plant floor to corporate planning systems.
Because of that, Keating says much of the training he provides at Peaslee Tech revolves around integration of various automation systems—becoming a proverbial jack of all trades. The more one knows, and the more flexible one can be moving from one system to another, the better.
“In automation, there’s a lot of integration,” he says. “You take an IT (information technology) person and make them electricians or take an electrician and make them an IT person. Lately, it’s been the latter.”
Keating says his programs typically contain about 40 hours of basic training with programmable logic controllers (PLCs), another 40 hours with an advanced controller, learning to go into a system and change code, 24 hours with a variable frequency drive, 25 hours on integration and 15 hours on an operator interface terminal.
“Peaslee is directed more to plant electricians, the more practical side,” he explains. “I have a teaching philosophy that I’m going to have every student come out of class with a basic working knowledge.”
Keating says he expects the field to continue to grow.
“People are realizing a four-year degree doesn’t guarantee financial security,” he says. “You can make as much (in an automation systems trade) and not go into debt while doing so.
“I see it as a growing field,” he adds. “The needs are going to keep growing as technology continues evolving.”
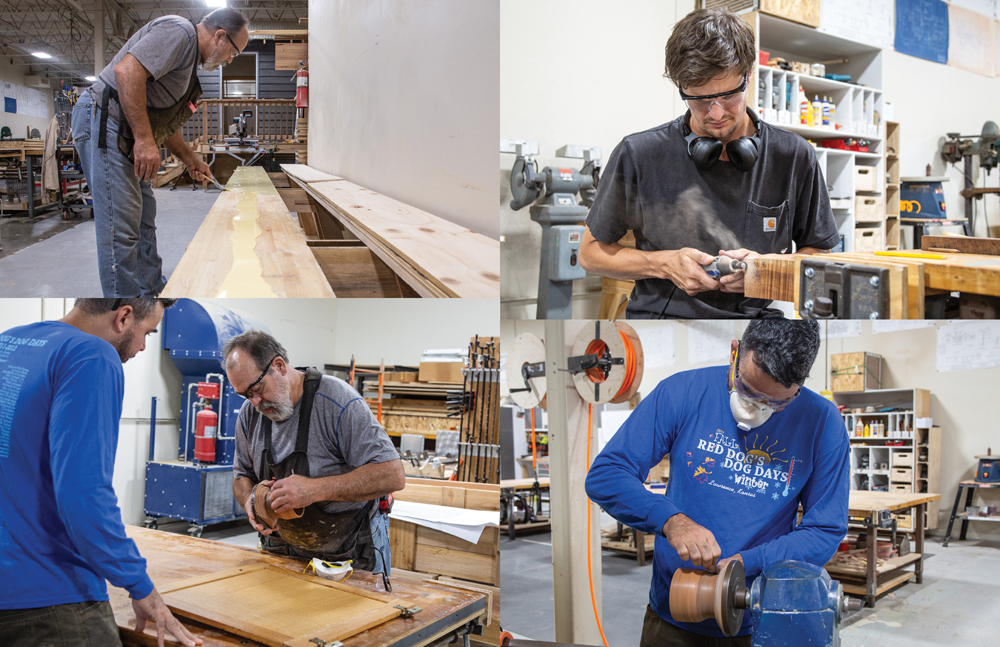
Carpentry and woodworking classes at Peaslee Tech
Carpentry/Woodworking
Jay Hundley says the supply of students coming to his classes wanting to learn to be carpenters and woodworkers runs hot and cold, and he should know. Before retiring and taking a job as a carpentry/woodworking instructor at Peaslee Tech, he worked as a high school woodshop teacher for 33 years, the last 21 at Lawrence High School.
“Overall, it’s stayed about the same,” Hundley says regarding interest in the trade. “Sometimes, you fill a class easily, but then only about half actually show up to take the class. Some sign up and are gophers on construction sites, and they don’t realize the time it takes and don’t last.
“A lot of students are older men and women trying to get remodeling skills so they can complete work around their houses. It runs the gamut,” he explains.
Anytime there’s a new technology that pops up, Hundley says older, traditional trades such as carpentry take a hit. After all, he says, carpentry is more physically laborious and often pays less than newer trade jobs like IT. Work is often done outdoors in poor conditions like rain or excessive heat or cold.
“Woodshop just is not sexy,” Hundley says. “Everyone knows what it takes. Physically, you’re going to live longer if you don’t do it. Construction is hard on you.”
That doesn’t mean Hundley is giving up on the trade that’s made his working life. Far from it. He says he combats negative perceptions of carpentry “one student at a time.” In the meantime, he instructs his Peaslee classes, which he says number 14 to 16 students to start, five to 9 by the end, with basic knowledge in rough framing, wood studs, installation of doors and windows, siding, building stairs, roofing and Sheetrock.
His last class in the spring built a tiny home inside the spacious woodshop at Peaslee. Once complete, the house will be moved onto a trailer and transported to a nearby Lawrence neighborhood to serve as low-cost housing.
Hundley says his class this fall will build the same thing and will use high school students from all around Douglas County.
“We have one or two already signed up,” he says. “I hope to get eight to 12, maybe even 15.”
Hundley says 90 percent of his courses take place in the shop. There’s very little in the way of classroom lectures.
“Most students in my class hate sitting in a chair and listening to a lecture,” he says. “I want to get them out working in the shop as soon as possible.”
That way, he says, students will gain basic skills that always will be in demand no matter where technology takes us next.
“There’s always going to be a need for carpenters,” Hundley adds.